La fabrication du cristal est un art ancestral. Quelle est sa composition ? Quels sont ses secrets de fabrication ? Quelles sont les techniques verrières utilisées pour réaliser de tels chefs-d'oeuvre ? Découvrons ensemble, à travers ce guide, les différentes étapes de la fabrication du cristal, de l'atelier à chaud en passant par l'atelier à froid.
De passage en Lorraine ? Ne manquez pas notre guide découverte, étape par étape, de nos célèbres cristalleries !
Qu'est-ce que le cristal ?
Subtile et délicate, la fabrication du cristal repose sur un secret, sa composition. Découvert pour la première fois par les Anglais en 1676, le cristal, à la différence du verre, contient du plomb.
En France, cette spécificité ne sera découverte qu’un siècle plus tard, par le directeur de la manufacture Saint-Louis, qui présentera cette innovation à l’Académie des Sciences.
Quelle est la composition du cristal ?
- 50% de sable appelé vitrifiant (plus ce pourcentage sera élevé, plus le verre sera résistant).
- 20% de potasse, également appelé le fondant.
- 24% au moins de plomb (c’est le stabilisant) suivant la législation Européenne (peut en contenir jusqu’à 32%).
- Quelques produits chimiques qui aident à la fusion.
VERRE | CRISTAL | |
Sable | 62% | 51,9% |
Minium de plomb | 24,8% | |
Soude | 18,6% | 3,1% |
Chaud | 7,3% | |
Potasse | 7% | 16% |
Barythe | 4% | 1,8% |
Borax | 0,7% | 1% |
Arsenic | 0,4% | 0,5% |
Zinc | 0,5% | |
Antimoine | 0,4% |
Quels sont les différents types de cristal ?
Verre ou cristal ? C’est donc la teneur en plomb qui détermine la nature du produit. La norme AFNOR distingue trois types de cristal :
- Entre 10 et 24% de minium de plomb, il s’agit de cristallin.
- Le cristal au plomb doit contenir 24% de minium de plomb.
- Le cristal supérieur dépasse les 30% (cristallerie Baccarat, Lalique et Saint-Louis).
Pourquoi ces éléments ?
La silice, principalement extraite du bassin parisien pour sa grande qualité, ne fond qu’à une température extrêmement élevée, son point de fusion est à hauteur de 1670°C. Malgré la technologie moderne de 2020, il est particulièrement onéreux en temps et en argent pour atteinte cette température au sein du four.
Cette situation était encore pire au Moyen Âge, où le verrier, nomade, alimentait son four à l’aide de bois, essentiellement du chêne et du hêtre (le bois sera remplacé par la houille).
Pour abaisser le point de fusion, un fondant est ajouté au mélange, permettant d’atteindre un point de fusion à 1400°C. Traditionnellement, il s’agissait de cendres de fougères, de bruyères ou de bois mort. Aujourd’hui, on utilise la soude, l’oxyde de potassium, l’oxyde de magnésium ou de calcin.
Le plomb, ajouté sous forme de minium, va offrir l’éclat au verre. Il le rend plus agréable à couper et à travailler pour le verrier.
Enfin, l’ajout d’oxydes métalliques ou de terres rares à la fabrication du cristal colore la matière : l’oxyde de cobalt donne du bleu, le manganèse donne une teinte améthyste, l’antimoine et l’arsenic offrent une couleur blanche opaque, l’uranium donne du jaune, et l’or le fameux rubis.
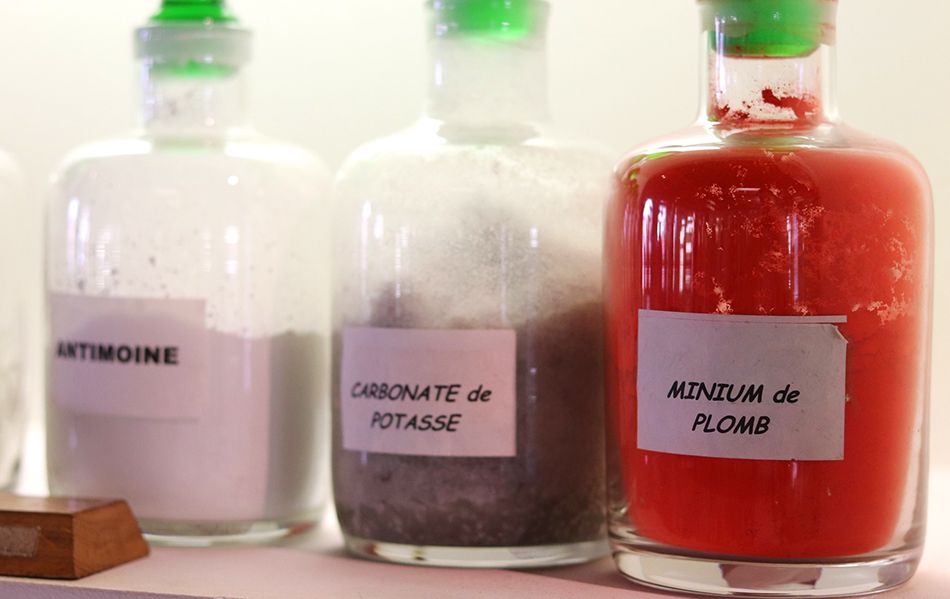
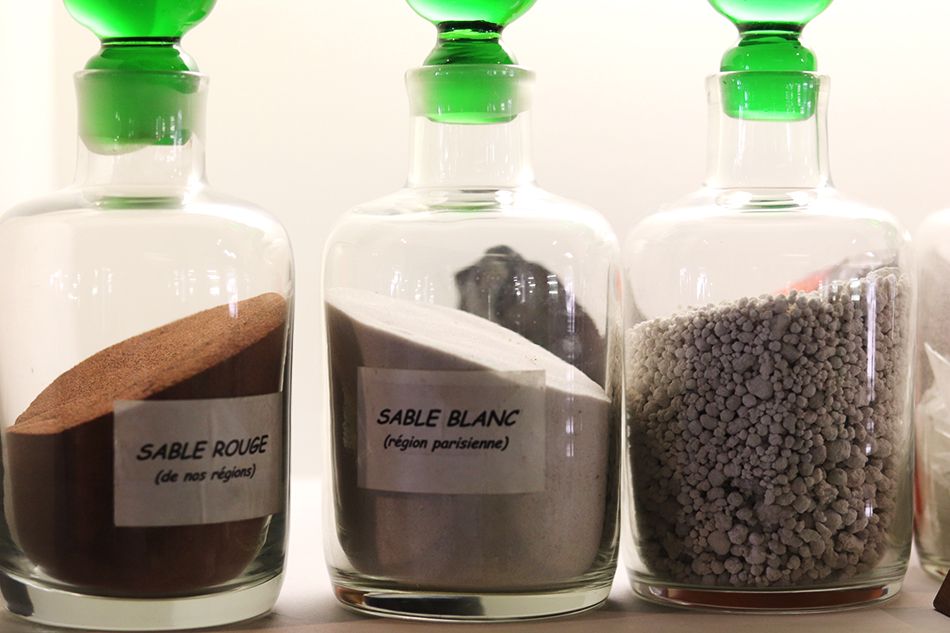
Mais attention, cette différence ne se résume pas simplement à une composition.
Le travail du cristal est toujours associé à la recherche d’une perfection, d’une pureté inégalée. C’est ainsi que la fabrication du cristal sera le plus souvent artisanale, mettant en valeur le travail de Meilleurs Ouvriers de France, alors que celle du verre sera le plus souvent mécanisée.
Le cristal est une poésie, un savoir-faire, l’artisan ressent alors le devoir de respecter la matière, son prestige, son passé. Le niveau d’exigence est alors élevé, à l’image des grandes cristalleries comme Baccarat, Lalique ou Saint-Louis, qui refusent presque une pièce sur deux, faute de qualité.
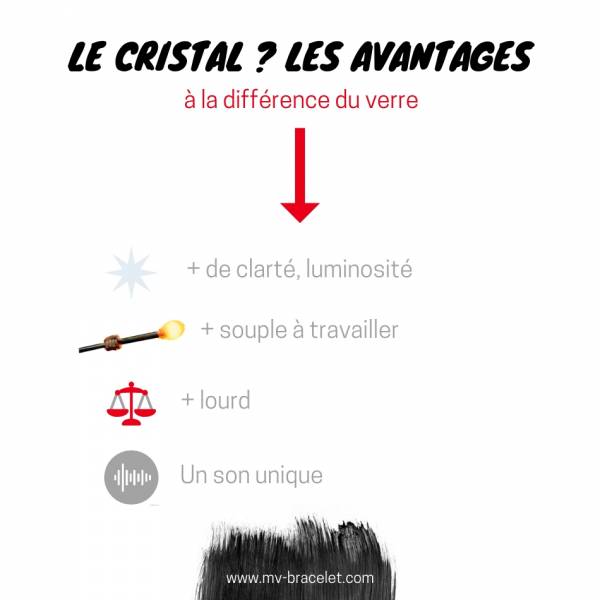
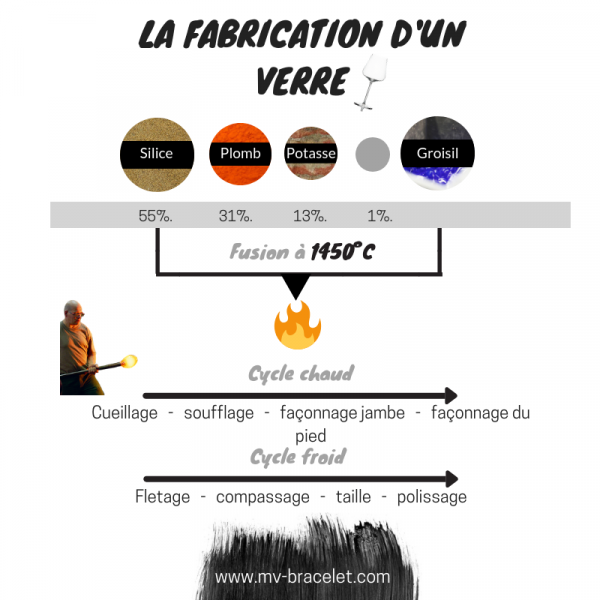
1) Le travail du verre à chaud
C’est la première étape de la fabrication du cristal. Elle fait la fierté de notre région, la Lorraine.
Le verre est transformé par soufflage après cueillage dans un four en fusion. À l’intérieur de ce dernier, le verre est à l’état liquide. Il devient visqueux entre 1100 et 800°C, puis dur à température ambiante. Le mélange vu précédemment se perd dans le feu pour renaître en un matériau encore informe.
Le four du verrier est la pièce emblématique autour de laquelle s’organise la vie de la cristallerie. Chaque verrier a sa mission, sa propre spécialité, bien précise, intervenant toujours au juste moment. C’est un véritable ballet hiérarchisé qui anime l’atelier à chaud du verre.
Le travail du souffleur de verre
Plusieurs ouvriers s’affairent autour du four pour sortir de la masse en fusion, à 1200°C, des boules rougeoyantes et fumantes. C’est une vraie chorégraphie. Les verriers vont et viennent entre le banc et le four, rythmant le façonnage à la température du verre.
Une fois la matière cueillie dans le four, le verrier lui donne une forme ronde en la centrant parfaitement grâce à sa mailloche. Il exerce une rotation continue et constante de sa canne, défiant l’attraction terrestre.
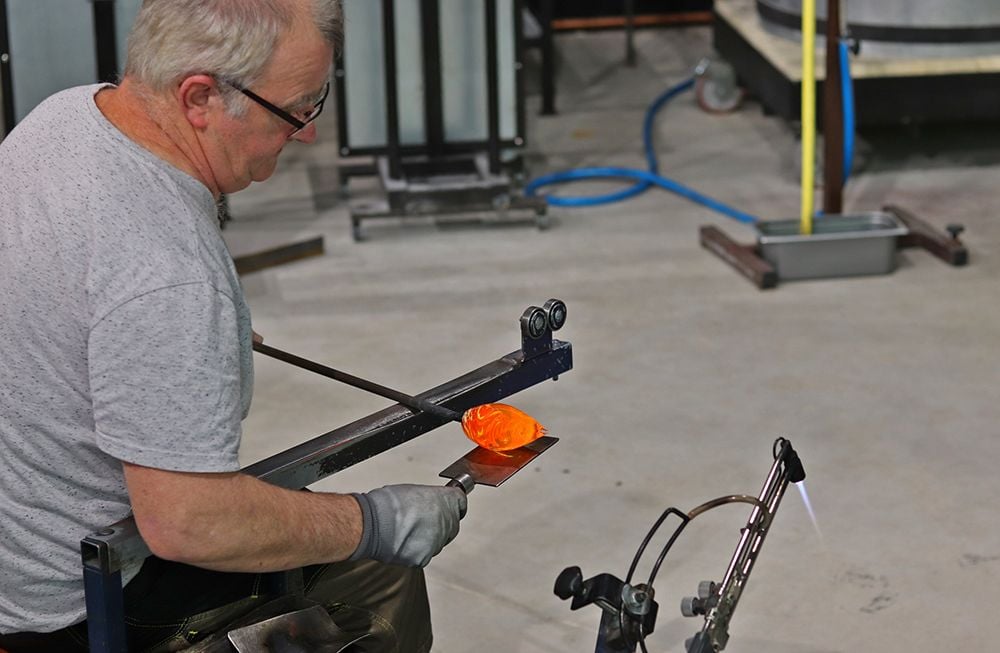
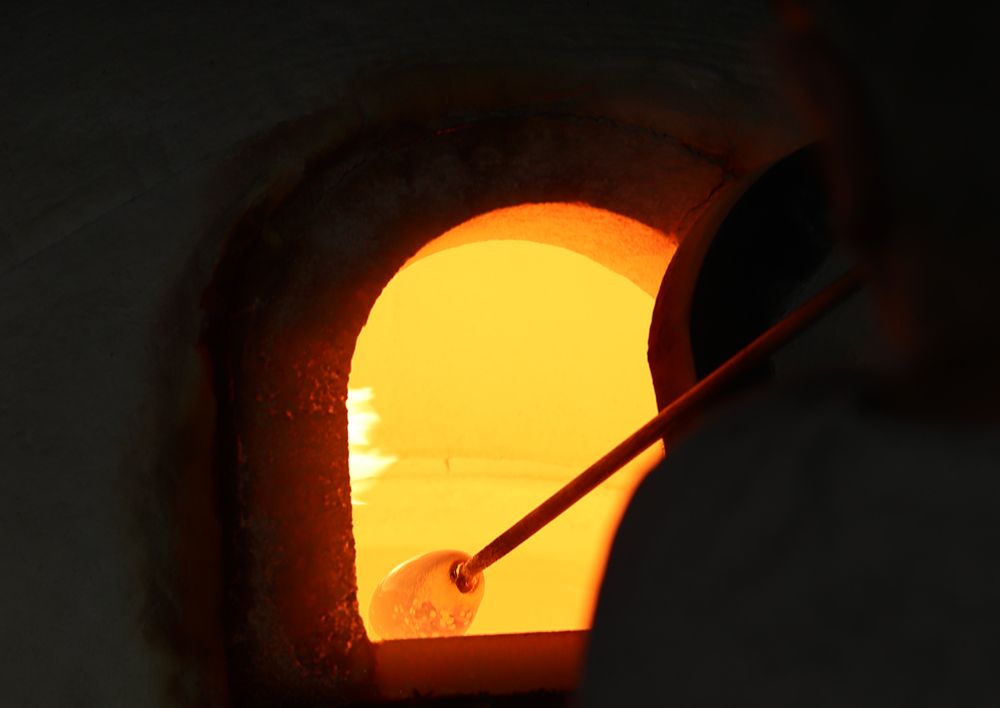
Le souffleur de verre introduit de l’air dans cette masse vitreuse en soufflant par la bouche dans sa canne creuse.
La pièce en cristal prend vie, le verrier effectue des mouvements de balancier pour l’agrandir et l’étirer. Un autre cueilleur peut apporter de la matière supplémentaire à la pièce. Le verrier va alors utiliser les ciseaux afin d’ajuster le pied du verre, ou pourquoi pas une anse. Il exécute l’opération de soufflage à l’intérieur d’un moule en foute dans le cas d’une pièce décorative.
Le moule du verrier
Pour la réalisation des pièces de série et sans resserrement, le moulage par pression est utilisé : on enferme une forme métallique autour de la masse en fusion qui se trouve ainsi repoussée contre les parois du moule.
Réaliser un moule nécessite une technicité est un savoir-faire pointu, la verrerie de Meisenthal était réputée pour ce savoir-faire du temps d’Émile Gallé.
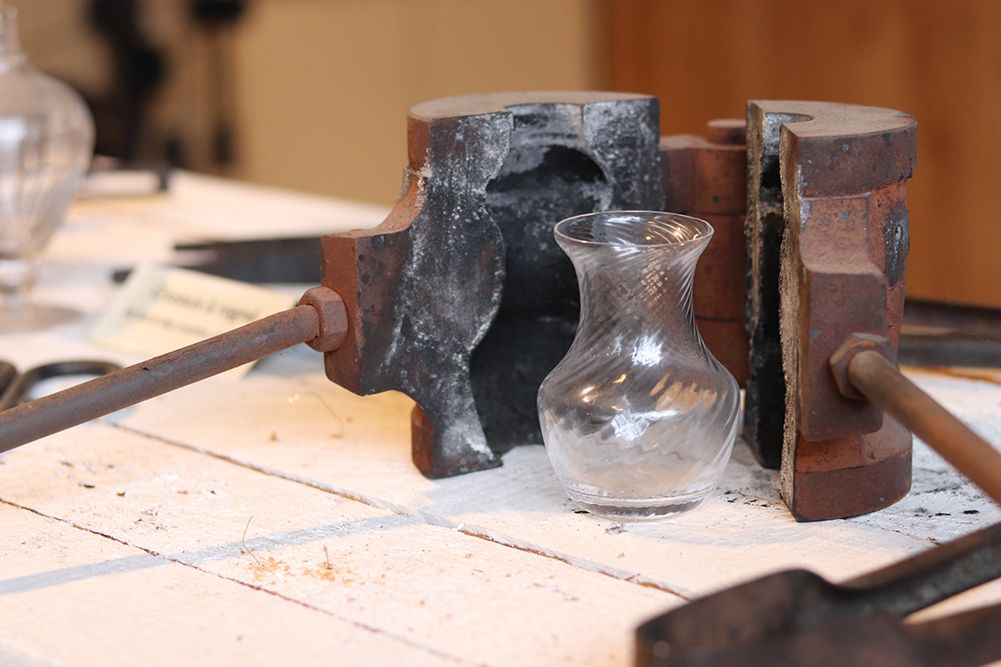
La recuisson finale
Le verre, contrairement aux autres arts du feu comme la céramique, exige un abaissement progressif de la température.
Une fois la pièce terminée, cette dernière doit passer sous un tunnel de recuisson, lui évitant tous risques de chocs thermiques et fêlures. Suivant le volume de la pièce, cette dernière va passer entre 12 heures et 96 heures dans ce tunnel à chaleur décroissante.
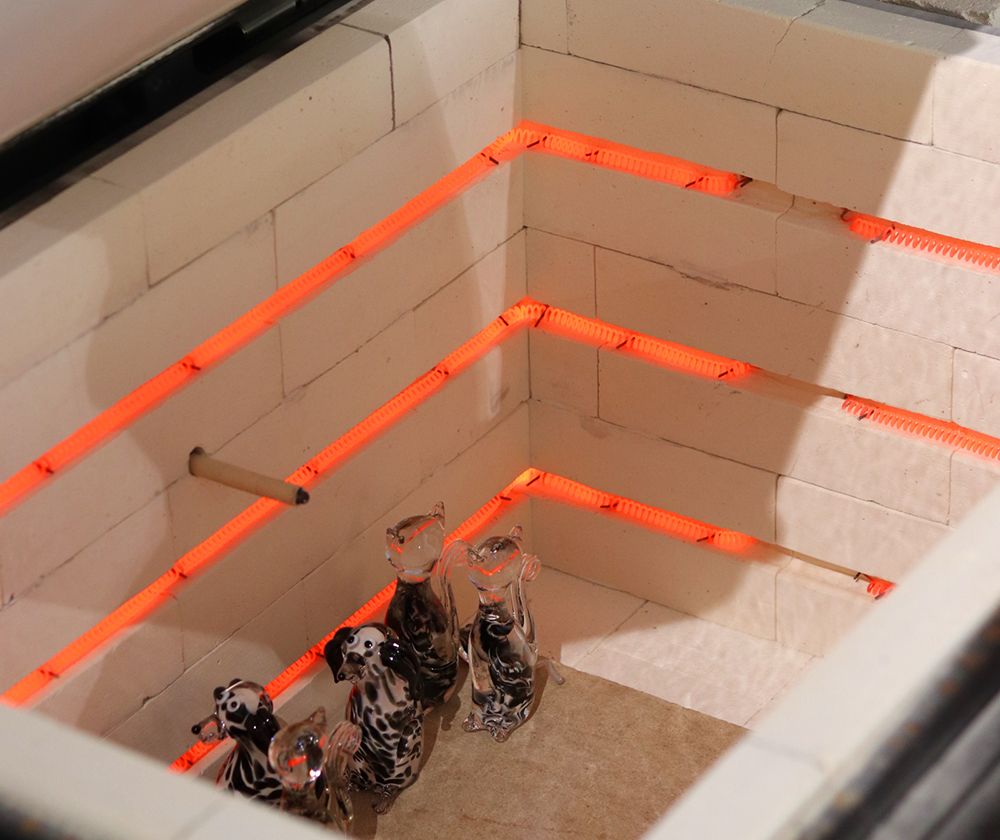
2) Le travail du verre à froid
Une fois l’objet refroidit, il peut être décoré et travaillé à froid. Les techniques sont multiples : gravures, tailles, dorure, émaillage …
L’une des plus pratiquée est la taille. Elle permet de réaliser des décors, mais surtout, elle permet de gommer les traces et défauts de l’atelier à chaud. Ainsi, la taille est réalisée à l’aide d’une meule électrique au grain plus ou moins fin en fonction de la finition désirée. Une fois taillé, le cristal présente un effet mat, sablé. La prochaine étape va lui rendre tout son éclat, c’est le polissage.
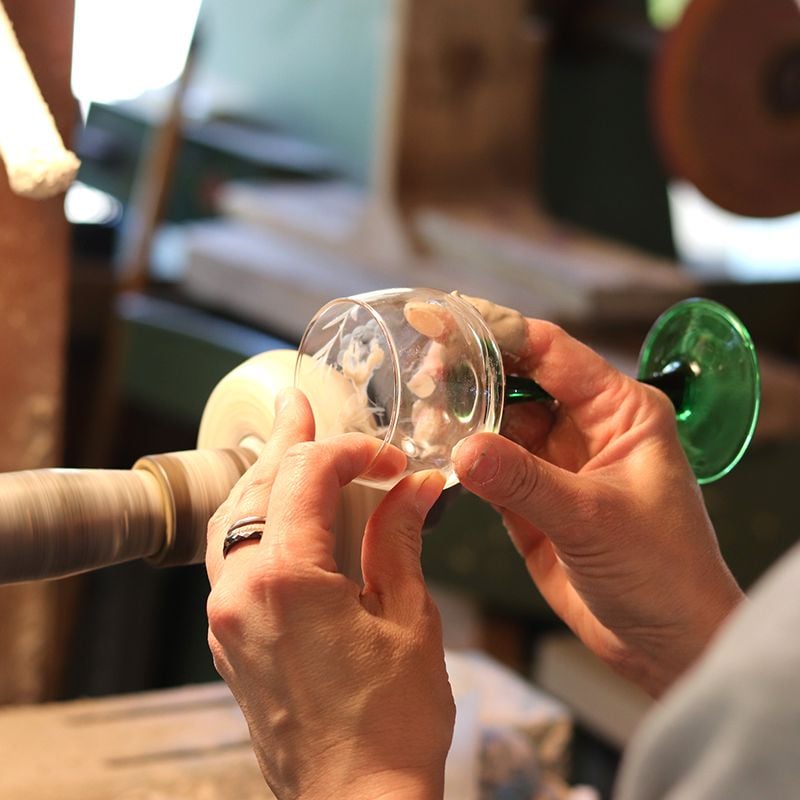
Dans l’exemple de la réalisation d’un verre, différentes étapes s’appliquent à l’atelier à froid :
- Le décalottage permet de supprimer la calotte par laquelle le verre était attaché à la canne (le haut du verre est alors très coupant).
- Le flettage meule la partie coupante, c’est-à-dire le buvant du verre.
- Enfin, afin d’adoucir le bord, le rendre arrondi et brillant, la dernière étape est le rebrûlage. Le verre est placé sur un plateau tournant et ses bords sont réchauffés.
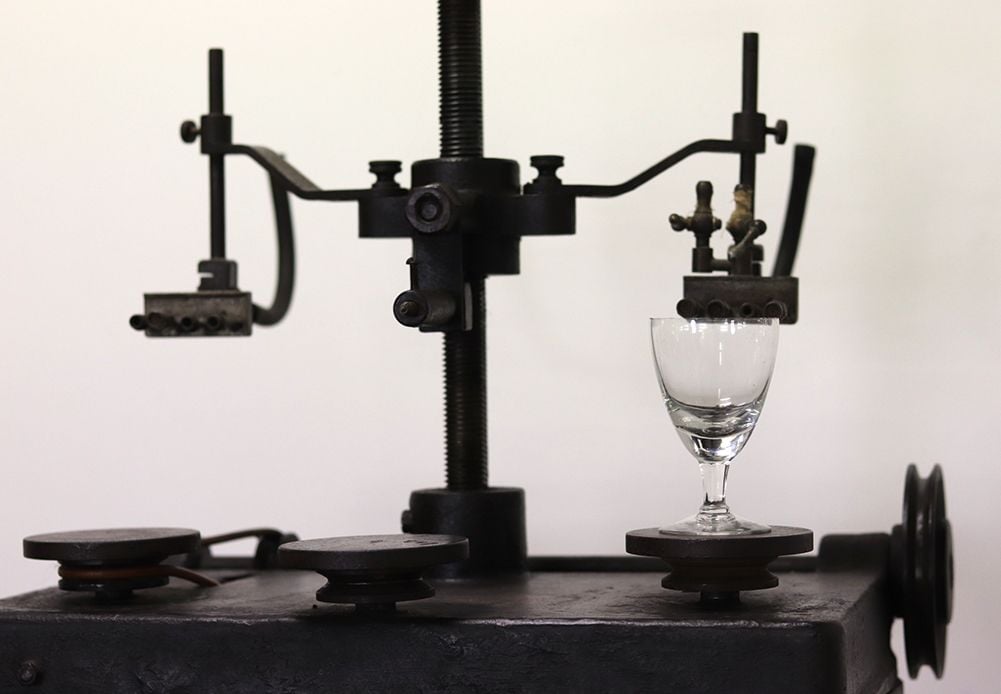
La peinture, l'émail et la dorure
La technique de la cire perdue
La technique de la cire perdue s’adresse aux pièces de prestige, à l’artistique. Cette technique verrière offre une parfaite représentation des différents détails que peut présenter une œuvre, rendu impossible à obtenir lors de l’utilisation d’un moule classique en fonte.
La manufacture Daum France maîtrise cette technique à la perfection. L’obtention d’une sculpture en pâte de cristal Daum nécessite de nombreuses étapes et l’intervention de nombreux artisans d’art, ce qui en justifie le prix élevé.
- Réalisation d’un modèle en plâtre.
- Réalisation d’un moule négatif en élastomère.
- Création de la pièce en cire grâce à ce dernier moule.
- Perfectionnement de la pièce.
- Aménagement d’une chape en plâtre autour de cette pièce.
- Placement de l’ensemble sous une étuve, laissant la cire s’évacuer, donnant naissance au moule final.
- Coulage des groisils à l’intérieur du moule.
L’artisan devra casser le moule pour découvrir l’œuvre. Elle sera ensuite perfectionnée grâce à l’action de polissage.
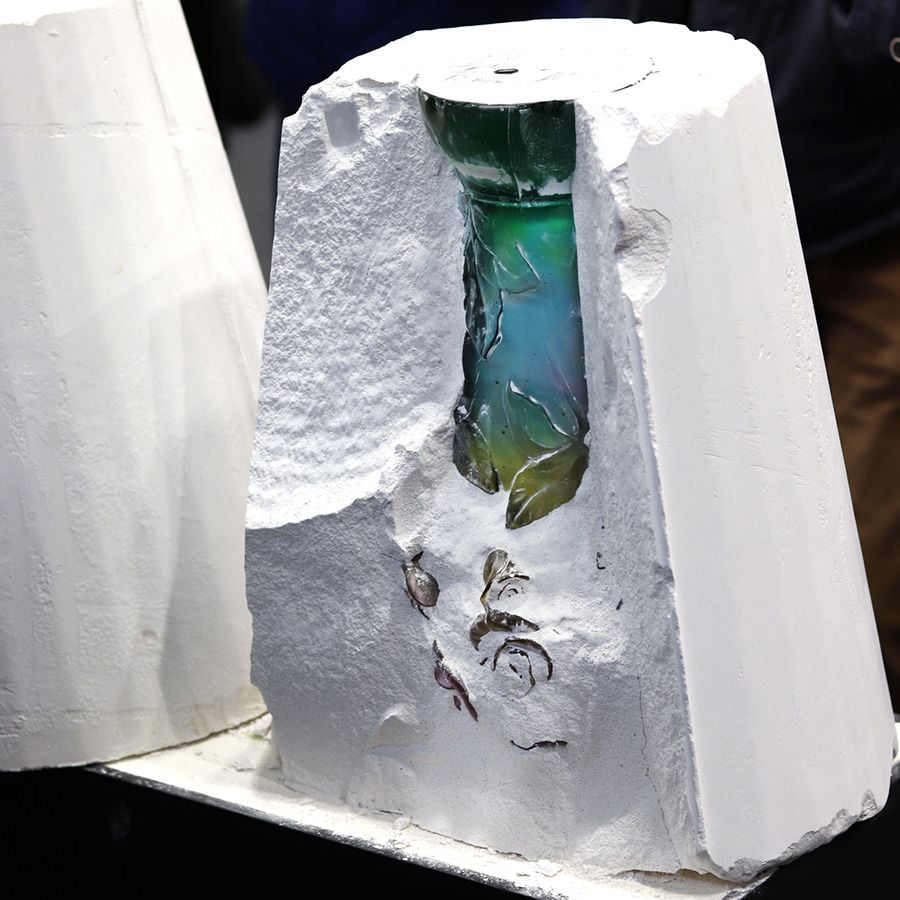
La technique du verre au chalumeau
Voici une autre technique verrière qui laisse place à une grande créativité. Notre collection de bracelet de perles, à l’instar du bracelet Croix de Lorraine utilise cette méthode.
La technique du verre au chalumeau permet de réaliser toutes sortes de figurines, sculptures, mais aussi différentes perles de verre, à l’instar de nos bracelets !
À l’aide d’une flamme directe, le verrier au chalumeau œuvre à partir de tubes ou de baguettes en verre qu’il ramollit et transforme par l’usage d’outils. Cette technique possède un grand avantage, le four traditionnel à pot n’est pas indispensable. Il est alors possible de commencer cette activité sans grand investissement. Cette activité regroupe un nombre important d’artisans passionnés qui se regroupent chaque année lors de festival !